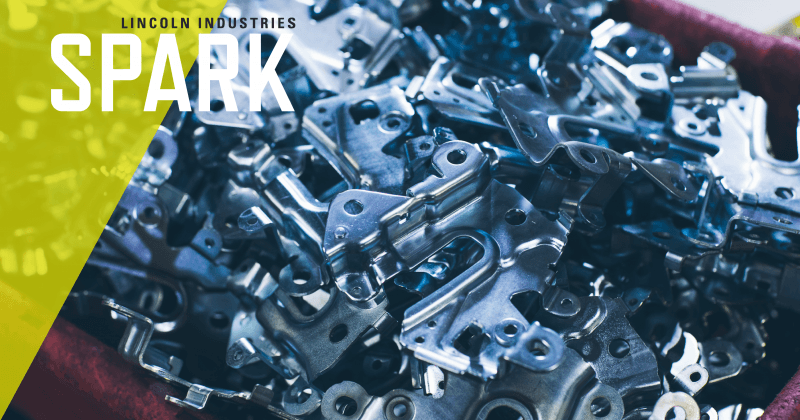
Lincoln Industries finishes and coatings provide cosmetic, heat management, protection, and functional solutions. Lincoln Industries partners with their customers on challenging finishing projects to enhance their products’ life, quality, and performance from concept to production. Zinc is a popular electroplating option for many industrial applications.
What is zinc plating, and what are the benefits?
- Zinc is a sacrificial coating-providing immense corrosion protection sacrificing itself before instead of the metal substrate that it’s protecting.
- It’s available in numerous colors.
- Zinc is easily applied to small parts such as fasteners in barrels or larger parts using our rack zinc process
- It’s compatible with different finishing processes and can be used as an additional level of corrosion protection with painted materials
One of the best ways to protect metal surfaces against corrosion is zinc. When you electroplate zinc onto ferrous metals, it creates a sacrificial layer, one of the main benefits of manufacturing. As a sacrificial coating, zinc breaks down sacrificially to ensure that the component’s substrate, or the metal under the coating, remains corrosion-free, meaning the coating sacrifices itself to protect the substrate.
When Lincoln Industries quotes parts for customers, they look at their prints and specifications. With the automated lines in their Lincoln, Nebraska facilities, they design specific recipes to meet performance requirements like salt spray and adhesion tests in addition to the cosmetic requirements.
What is the zinc plating process?
- Cleaning the surface or part-to get proper adhesion of the zinc plating, it’s essential to clean the surface of the part/substrate.
- Preparing the plating solution-zinc plating requires a specially formulated electrolyte solution called a plating bath. Plating baths can help produce the finished product’s desired chemical and physical properties, including acid zinc and alkaline zinc.
- The part’s size and shape determine the zinc plating procedure (rack vs. barrel)-choosing the proper way to plate the parts. Lincoln Industries team members use rack plating by affixing more significant parts to metal racks that run on an automatic plating line through a series of plating baths. Barrel plating is used for smaller or intricate pieces to rotate in the barrel providing a uniform finish.
- Electrical current-electroplating uses an electrical current to deposit metal ions onto the surface of the substrate/part. With zinc plating, the substrate is the cathode. A DC originating at the anode is introduced into the bath and flows to the substrate. The zinc ions are then deposited onto the surface.
- Post plate bake application- A post plate bake application is applied after the plating process to remove the hydrogen embrittlement.
Lincoln Industries coatings are trivalent passivate, which complies with RoHS and REACH standards and is better for the environment.
Lincoln Industries Rack Line Standards:
- Capable of handling parts 114” long, 50” high, by 26” wide
- Excellent for long, large quantity runs
- House systems provide great flexibility
- Three different chromates can run at the same time, which provides efficiencies.
Quality Assurance:
- Strict adherence to Statistical Process Control (SPC)
- Constantly monitored for consistent high quality
- Coatings are to ASTM B633 Standards
At Lincoln Industries, customization for the customer’s needs is what we do. We offer zinc plating for many projects and parts, from nuts, bolts, brackets to other essential and unique products. Our zinc plating process is a preferred choice for its excellent corrosion protection. If you’re looking for peace of mind in choosing your zinc plater, you can have confidence in Lincoln Industries and their 65+ years of business. Contact us today to learn more about the benefits of zinc plating and our other services to fit your needs.
Founded in 1952, Lincoln Industries has grown into the nation’s largest and most diverse privately-held metal finishing company. We provide solutions to premium OEMs in heat management, corrosion, wear, performance and cosmetics. Our expertise includes metal finishing, coatings, tube fabrication, supply chain management, machine build, and design and engineering. Over 69 years, we’ve developed strong relationships with companies like Harley Davidson, PACCAR, Volvo, Navistar, Graco, and Cummins. Known for our unique company culture, Lincoln Industries has been named one of the 25 Best Medium-Sized Companies to Work for in America seven times.