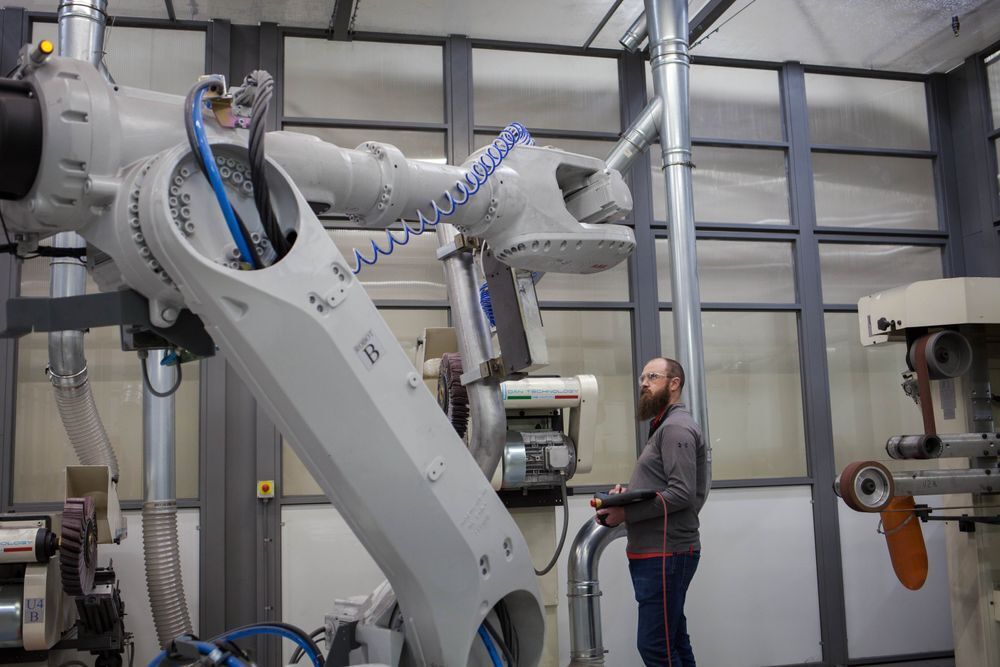
How an Italian-made Robotic Polishing Cell is Progressing Polishing Proficiency
Lincoln Industries has embarked on a journey to advance our polishing approach through the introduction of a robotic polishing cell for large diameter exhaust stacks. This significant investment, which took over a year of engineering, design, and construction, represents a major stride in automating a previously manual process. This change is not just about embracing technology; it’s about shaping the future of metal finishing for the trucking industry.
The decision to invest in automation stemmed from multiple strategic objectives. It enhanced safety by addressing ergonomic challenges associated with handling large diameter tubes. It was also crucial to improve consistency in output while boosting productivity. Most importantly, it expanded critical capacity, setting the stage for future growth with trucking customers.
The heart of this advancement lies in the dual robot polishing cell developed by Lincoln Industries and DAN technology. The dual robot setup allows for flexibility in processing of parts by allowing the robots to work independently or as a team to optimize the flow of different parts through the cell. These robots are dedicated to polishing large-diameter tubes in preparation for nickel chrome plating.
The efficiency brought by this automation has freed operators from the physically demanding task of manual polishing allowing them to focus on less ergonomically challenging parts. This shift has not only improved safety standards but also improved overall productivity.
For Class 8 truck customers, this means increased capacity for their planned growth enabling them to rely on Lincoln Industries for consistent, high-quality products as they expand.
In navigating the challenges of integrating such a complex robotic polishing cell, Lincoln Industries required exceptional project management and adaptability. Throughout the process the engineering and operations teams worked with DAN to design the custom cell to meet our needs. This culminated in a trip to Italy for machine run-off to ensure all specifications were met. And despite supply chain disruptions and extended lead times, the team made necessary adjustments to ensure the successful and timely completion of the project.
2024 will bring additional automation opportunities and investments with a fully automated muffler polishing cell coming online. Moving forward, Lincoln Industries remains dedicated to looking for ways to elevate our standards through continuous improvement and automation, allowing us to better support our customers.